研磨工場
ボウル自動研磨機の局排導入事例
お客様の要望事項
作業環境改善のため集塵機を導入したいが、作業によって機械のセットを移動しなければならないため、全体を囲うこともできず特定の場所にフードを設置することもできないということでした。
また、費用を掛けずに実現したいという要望もありました。
導入前
ボール(厨房用品)を自動研磨する機械が複数台稼働しているが、これまで集塵機はなく、粉じんが工場内に飛散していました。
作業者はマスクをして作業しているが、夕方になると黒くなっていました。
導入後
今回は最小限の風量設定で集塵機を選定しました。
粉じんの飛散を極力減らし集塵効率を上げるためには出来る限り機械を囲うのがポイントですが、それはお客様の方で段ボールにて塞ぐことになりました。
当社は集塵機の設置とダクト接続を施工しました。
フードは設置せず、ダクトホースの開口を粉塵発生源に近づけて集塵することにしました。
結果的には集塵機がなかった時と比べると大幅な環境改善になり、粉塵の飛散や臭いが軽減されてお客様にも満足いただけました。
サイクロン集塵機入れ替え事例
研磨工場のサイクロン式集塵機が老朽化したので更新しました。
更新年月:2016年10月
- 送風機1973年製 サイクロン1990年製
- 風量 400m3/min
導入前
以下の問題を抱えていました。
- ダクト、サイクロン共に錆びて多数の穴が開いており、空気漏れがたくさんある。
- 粉塵取り出し扉の空気漏れがあり、捕集した粉塵が外部に漏れている。
- 送風機のベルトのスリップがあり所定の回転数が得られていない。
- 送風機のバランスが崩れており、振動、騒音が大きい。
- 実際に(フードにて)風量を測定すると240m3/minしか出ていなかった。
- それにより風量不足となり、研磨作業の作業環境が悪くなっている。
- 37kW送風機を使用していた。
↓
導入後
- 新規のサイクロン、ダクトおよび送風機に全面リニューアル。
- 送風機はコストの都合上30kWに変更したが、圧損計算を行いダクト径や経路の適正化を行うことで、据付後に測定したところ430m3/minと十分な風量が得られた。
- 送風機の騒音、振動も低くなりました。
- 研磨作業に適した風量が出るようになり、作業場での粉塵の飛散が軽減されました。
バフ研磨作業場の集塵機導入
お客様からのご要望
この工場ではチタンとステンレスをバフレースにより研磨しているが、これまでは一つの集塵機にて両方の粉塵を集塵していた。
しかし、集塵機のメンテナンス性向上と廃棄物の純度を高めるためステンレス用の集塵機とチタン用の集塵機で使い分けることとなり、集塵機を増設したい。
また、工場内のスペースを有効活用するために屋内にあった既存の基幹ダクトを屋外に移設したい。
導入前
屋内に基幹ダクトが通っており、一つのバフレースにつきダクトホースが上下1本ずつ伸びているのみであった。
↓
導入後
基幹ダクトは屋外に移設したため屋内の有効スペースが広くなった。
バフレースにホース先端を差し込むだけの着脱方式とし、簡単にチタンとステンレスの段取り替えが出来るようにした。
集塵機増設を行い新規のダクトも這わせることとなるが、他設備の関係から客先要望によりダクト経路が少し複雑にせざるを得なかった。
どのような形でも施工は可能ですが、本来であればもっとすっきりした経路での提案を行い、集塵能力を最大限引き出すことが可能です。
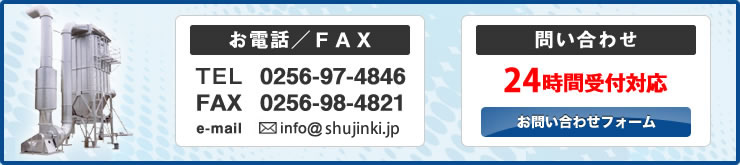